Titanium alloy forging heating process
Low thermal conductivity of titanium, heating the main difficulties are: the use of surface heating method, the heating time is very long. Large billet heating, cross-section temperature difference. The thermal conductivity of titanium alloys increases with increasing temperature.
The second characteristic of titanium heating is that they react strongly with air when the temperature is increased. Titanium reacts strongly with oxygen when heated above 650 C and also with nitrogen when above 700 C while forming a deeper surface layer saturated with both gas. For example, when a 350 mm-diameter titanium ingot is heated to 1100 to 1150 by surface heating, it is necessary to keep the temperature in a temperature range in which titanium strongly reacts with gas for more than 3 to 4 hours to form an gettering layer with a thickness of 1 mm or more. This getter layer can degrade the deformation properties of the alloy.
Hydrogen absorption is particularly stark when heated in an oil furnace with a reducing atmosphere, and hydrogen diffuses into the interior of the alloy during heating to reduce the plasticity of the alloy. Hydrogen absorption of titanium alloys slows significantly when heated in an oil furnace with an oxidizing atmosphere; hydrogen absorption is slower when heated in a typical box electric furnace.
It can be seen. Titanium alloy blank should be heated in an electric furnace. When you just have to use the flame heating, the atmosphere should be micro-oxidation of the furnace, so as not to cause hydrogen embrittlement. No matter what kind of furnace heating, the titanium alloy should not have a role with the refractory, the bottom of the furnace should be placed on a stainless steel plate. Do not use more than 50% nickel content of heat-resistant alloy plates, in order to avoid welding the bank on the board.
In order to make forgings and forgings to achieve uniform fine grain structure and high mechanical properties, heating, you must ensure that the blank in the shortest residence time at high temperature. Therefore, in order to solve the problem of low thermal conductivity of titanium alloy during heating and serious aspiration at extreme temperature, staged heating is usually adopted. In the first stage, the slab is slowly heated to 650-700 C and then rapidly heated to the desired temperature. Because titanium has less getter below 700 C, segmented heating oxygen has a much lower overall permeation effect than metal in general.
Staged heating can be used to shorten the dwell time at elevated temperatures. Although titanium has a low thermal conductivity at low temperatures, it has a similar thermal conductivity to steel at high temperatures, so titanium can be heated to high temperatures faster than steel when heated to 700 C.
For precision forgings requiring high surface quality, or forgings with small margins (eg compressor blades, plates, etc.), the billet is best heated in a protective atmosphere (argon or helium), but this investment is large and cost High and there is a risk of air pollution after it is released. Therefore, glass-coated lubricant coating is often used in production and then heated in a common box-type resistance furnace. Glass lubricant cannot only prevent the formation of oxide scale black surface, but also reduce the thickness of α layer, and can play a role in lubrication during the deformation.
If the job is interrupted for a short time, the temperature of the furnace with the billet should be lowered to 850 C. When the operation is continued. The furnace temperature is re-raised to the initial forging temperature at the rate of furnace power. When the work is suspended for a long time, the billet should be taken out and cooled on asbestos or dry sand.
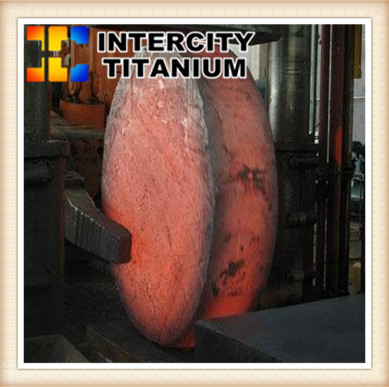
Low thermal conductivity of titanium, heating the main difficulties are: the use of surface heating method, the heating time is very long. Large billet heating, cross-section temperature difference. The thermal conductivity of titanium alloys increases with increasing temperature.
The second characteristic of titanium heating is that they react strongly with air when the temperature is increased. Titanium reacts strongly with oxygen when heated above 650 C and also with nitrogen when above 700 C while forming a deeper surface layer saturated with both gas. For example, when a 350 mm-diameter titanium ingot is heated to 1100 to 1150 by surface heating, it is necessary to keep the temperature in a temperature range in which titanium strongly reacts with gas for more than 3 to 4 hours to form an gettering layer with a thickness of 1 mm or more. This getter layer can degrade the deformation properties of the alloy.
Hydrogen absorption is particularly stark when heated in an oil furnace with a reducing atmosphere, and hydrogen diffuses into the interior of the alloy during heating to reduce the plasticity of the alloy. Hydrogen absorption of titanium alloys slows significantly when heated in an oil furnace with an oxidizing atmosphere; hydrogen absorption is slower when heated in a typical box electric furnace.
It can be seen. Titanium alloy blank should be heated in an electric furnace. When you just have to use the flame heating, the atmosphere should be micro-oxidation of the furnace, so as not to cause hydrogen embrittlement. No matter what kind of furnace heating, the titanium alloy should not have a role with the refractory, the bottom of the furnace should be placed on a stainless steel plate. Do not use more than 50% nickel content of heat-resistant alloy plates, in order to avoid welding the bank on the board.
In order to make forgings and forgings to achieve uniform fine grain structure and high mechanical properties, heating, you must ensure that the blank in the shortest residence time at high temperature. Therefore, in order to solve the problem of low thermal conductivity of titanium alloy during heating and serious aspiration at extreme temperature, staged heating is usually adopted. In the first stage, the slab is slowly heated to 650-700 C and then rapidly heated to the desired temperature. Because titanium has less getter below 700 C, segmented heating oxygen has a much lower overall permeation effect than metal in general.
Staged heating can be used to shorten the dwell time at elevated temperatures. Although titanium has a low thermal conductivity at low temperatures, it has a similar thermal conductivity to steel at high temperatures, so titanium can be heated to high temperatures faster than steel when heated to 700 C.
For precision forgings requiring high surface quality, or forgings with small margins (eg compressor blades, plates, etc.), the billet is best heated in a protective atmosphere (argon or helium), but this investment is large and cost High and there is a risk of air pollution after it is released. Therefore, glass-coated lubricant coating is often used in production and then heated in a common box-type resistance furnace. Glass lubricant cannot only prevent the formation of oxide scale black surface, but also reduce the thickness of α layer, and can play a role in lubrication during the deformation.
If the job is interrupted for a short time, the temperature of the furnace with the billet should be lowered to 850 C. When the operation is continued. The furnace temperature is re-raised to the initial forging temperature at the rate of furnace power. When the work is suspended for a long time, the billet should be taken out and cooled on asbestos or dry sand.
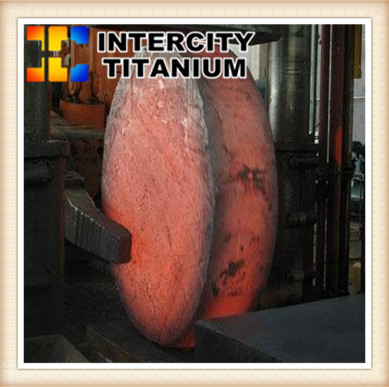