Titanium pump casting process
Due to poor casting performance of titanium, cast titanium casting mold setting is particularly important, if by casting cobalt-chromium alloy, stainless steel vertical casting method, often casting incomplete. Titanium casting surface treatment is very important, due to the special physical properties of titanium, such as the thermal conductivity of titanium is small, the surface hardness and low modulus of elasticity, viscosity, low conductivity, easy oxidation, which titanium surface treatment Brought great difficulty, the conventional surface treatment method used is difficult to achieve the desired effect, we must use special processing methods and means of operation. Casting titanium casting mold has the following requirements:
Casting diameter to be coarse (not less than 4mm) and short, to ensure that there is a sufficient amount of titanium solution, after the shortest way into the mold cavity; cast and melt connection should be appropriately bold; the number of sprue should be 3 ~ 4; parallel interpolation can be used, but also available lateral interpolation; to avoid the formation of right angles. The effect of the Second Mold Temperature on the Surface Properties of Titanium Castings. Titanium solution by the embedding material pollution, in addition to the melting chamber and the degree of vacuum embedding material composition, but also with the mold temperature. When the mold temperature is high, the titanium liquid easily reacts with the embedding material. Elements such as Zr, Al and Si easily diffuse into the titanium matrix to form interstitial elements and form thicker hardened layers, so that the tensile strength and yield Increased strength, ductility, increased brittleness. Among them, the increase of oxygen content changes the mechanical properties of castings most obviously. When the mold temperature is small, the hardened layer also becomes thinner. However, when the mold temperature is depressed, the casting flow rate is affected. Therefore, it is necessary to select the mold temperature appropriately, and sometimes the mold temperature can be identified according to different purposes.
Titanium pump casting process
Owing to the limited amount of melting of the vacuum condensate hearth furnace in China, the knot casting has brought difficulties. In order to save liquid titanium, the top-pouring process is adopted.
① Model processes design: mold for machining graphite type, composed of 12 blocks. Mold design is affordable, to achieve the desired goal.
② Pouring melting process: Although the mold after the vacuum degassing, but because the mold and the core larger pouring will still emit gas, if the gas cannot be discharged from the cavity in time, it will make castings appear porosity defects. In order to solve this problem.
③ In the pump case spiral flow split ribs designed to balance the radial force, especially for large flow high-lift pump. However, due to its existence, the design and manufacture of knotted cores have brought serious difficulties. In order to prevent future degassing and pouring process from breaking, reinforcement measures should be taken.
Titanium pump post-surface treatment is not only to get a smooth and smooth surface, reducing the accumulation of food and plaque, etc., to maintain the patient's normal oral micro-ecological balance, but also increased the beauty of the denture; more important It is through these surface treatment and modification process to improve the surface properties and adaptability of titanium castings to improve the physical and chemical properties such as wear resistance, corrosion resistance and stress fatigue resistance of the denture.
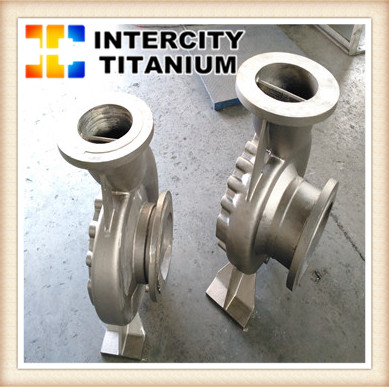
Due to poor casting performance of titanium, cast titanium casting mold setting is particularly important, if by casting cobalt-chromium alloy, stainless steel vertical casting method, often casting incomplete. Titanium casting surface treatment is very important, due to the special physical properties of titanium, such as the thermal conductivity of titanium is small, the surface hardness and low modulus of elasticity, viscosity, low conductivity, easy oxidation, which titanium surface treatment Brought great difficulty, the conventional surface treatment method used is difficult to achieve the desired effect, we must use special processing methods and means of operation. Casting titanium casting mold has the following requirements:
Casting diameter to be coarse (not less than 4mm) and short, to ensure that there is a sufficient amount of titanium solution, after the shortest way into the mold cavity; cast and melt connection should be appropriately bold; the number of sprue should be 3 ~ 4; parallel interpolation can be used, but also available lateral interpolation; to avoid the formation of right angles. The effect of the Second Mold Temperature on the Surface Properties of Titanium Castings. Titanium solution by the embedding material pollution, in addition to the melting chamber and the degree of vacuum embedding material composition, but also with the mold temperature. When the mold temperature is high, the titanium liquid easily reacts with the embedding material. Elements such as Zr, Al and Si easily diffuse into the titanium matrix to form interstitial elements and form thicker hardened layers, so that the tensile strength and yield Increased strength, ductility, increased brittleness. Among them, the increase of oxygen content changes the mechanical properties of castings most obviously. When the mold temperature is small, the hardened layer also becomes thinner. However, when the mold temperature is depressed, the casting flow rate is affected. Therefore, it is necessary to select the mold temperature appropriately, and sometimes the mold temperature can be identified according to different purposes.
Titanium pump casting process
Owing to the limited amount of melting of the vacuum condensate hearth furnace in China, the knot casting has brought difficulties. In order to save liquid titanium, the top-pouring process is adopted.
① Model processes design: mold for machining graphite type, composed of 12 blocks. Mold design is affordable, to achieve the desired goal.
② Pouring melting process: Although the mold after the vacuum degassing, but because the mold and the core larger pouring will still emit gas, if the gas cannot be discharged from the cavity in time, it will make castings appear porosity defects. In order to solve this problem.
③ In the pump case spiral flow split ribs designed to balance the radial force, especially for large flow high-lift pump. However, due to its existence, the design and manufacture of knotted cores have brought serious difficulties. In order to prevent future degassing and pouring process from breaking, reinforcement measures should be taken.
Titanium pump post-surface treatment is not only to get a smooth and smooth surface, reducing the accumulation of food and plaque, etc., to maintain the patient's normal oral micro-ecological balance, but also increased the beauty of the denture; more important It is through these surface treatment and modification process to improve the surface properties and adaptability of titanium castings to improve the physical and chemical properties such as wear resistance, corrosion resistance and stress fatigue resistance of the denture.
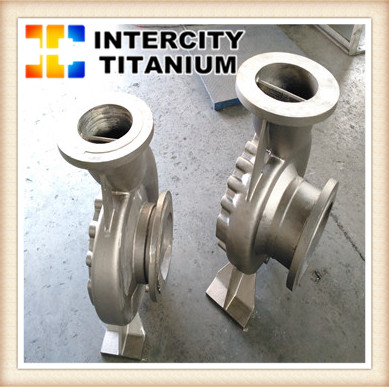