Titanium rod production process
Titanium rods the traditional process is to cast titanium sponge into ingots, and then through the billet, forging mill to produce a titanium rod. Titanium sponge is the most primitive material in the production of titanium, which is melted to get the titanium material processing of the initial material - titanium ingot.
Titanium rods from titanium sponge to the rough machining process is as follows:
(1) the piezoelectric electrode, the sponge titanium through the press electrode, the formation of dense sponge titanium pressed block electrode;
(2) vacuum casting, under the condition of 1700-1800 DEG C and -103Pa, performing three vacuum casting on the sponge titanium pressed block electrode;
(3) billets, at 1000 ℃ under the conditions of the hydraulic billets, the final pressure into a square billet;
Billet should be noted that because of the pressure and reduce the life of the titanium rod, so when closed die forging method forging titanium rods, closed die forging must strictly limit the size of the original rough, which makes the preparation process is complicated. Whether to use closed dies forging, from both interest and process feasibility considerations. Open die forging, burr loss accounted for 15% -20% of the rough weight of the workpiece holding part of the waste (if you press the forging conditions must retain this part) 10% of the weight of the blank The relative loss of flash metal is usually blank The weight loss increases, some of the structure is asymmetric, larger cross-sectional area and difficult to fill the local forgings, burrs up to 50% of the cost of closed die forging without burr loss, but the process complexity of the billet, you need to add more Multi-transition groove, will undoubtedly increase auxiliary costs.
Then only the final heat treatment and cutting the coarse. Forging temperature and degree of deformation are to determine the alloy structure, the basic factor of performance. Heat treatment of titanium rods and heat treatment of steel is distinct from the forging is usually used to make shapes and sizes close to the waste. The organization of the alloy cannot play a decisive role. Therefore, the final step of titanium rod process specifications has a particularly important role. It is necessary to make the overall deformation of the blank not less than 30% of the deformation temperature does not exceed the phase transition temperature, in order to make the titanium rod at the same time to obtain higher strength and plasticity and should strive to temperature and degree of deformation throughout the deformation of the rough as possible.
(4) the first rolling, at 970 ~ 980 ℃ under the conditions of a preliminary mill rolling into a cylindrical shape blank;
(5) The second rolling, under the conditions of 950, rolling into a bank in a rolling mill.
There are many rolling methods that can be ranked according to different characteristics. Extruded by metal flow and deformation characteristics of classification, a positive extrusion, reverse extrusion and special extrusion. Special extrusion includes hydrostatic extrusion, continuous extrusion, lateral extrusion, co-extrusion, coextrusion, sheath extrusion, peeling extrusion, water seal extrusion, bitter extrusion, powder extrusion, semi Melt Extrusion, liquid extrusion and the like. Extrusion by temperature classification, hot extrusion, warm extrusion and cold extrusion. Hot extrusion and cold extrusion are the two major branches of extrusion, the main application in the metallurgical industry hot extrusion, which is commonly known as the extrusion; mechanical industrial system application of cold extrusion; warm extrusion development relatively late, the scope of application is small .
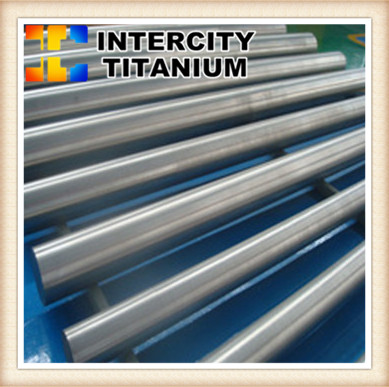
Titanium rods the traditional process is to cast titanium sponge into ingots, and then through the billet, forging mill to produce a titanium rod. Titanium sponge is the most primitive material in the production of titanium, which is melted to get the titanium material processing of the initial material - titanium ingot.
Titanium rods from titanium sponge to the rough machining process is as follows:
(1) the piezoelectric electrode, the sponge titanium through the press electrode, the formation of dense sponge titanium pressed block electrode;
(2) vacuum casting, under the condition of 1700-1800 DEG C and -103Pa, performing three vacuum casting on the sponge titanium pressed block electrode;
(3) billets, at 1000 ℃ under the conditions of the hydraulic billets, the final pressure into a square billet;
Billet should be noted that because of the pressure and reduce the life of the titanium rod, so when closed die forging method forging titanium rods, closed die forging must strictly limit the size of the original rough, which makes the preparation process is complicated. Whether to use closed dies forging, from both interest and process feasibility considerations. Open die forging, burr loss accounted for 15% -20% of the rough weight of the workpiece holding part of the waste (if you press the forging conditions must retain this part) 10% of the weight of the blank The relative loss of flash metal is usually blank The weight loss increases, some of the structure is asymmetric, larger cross-sectional area and difficult to fill the local forgings, burrs up to 50% of the cost of closed die forging without burr loss, but the process complexity of the billet, you need to add more Multi-transition groove, will undoubtedly increase auxiliary costs.
Then only the final heat treatment and cutting the coarse. Forging temperature and degree of deformation are to determine the alloy structure, the basic factor of performance. Heat treatment of titanium rods and heat treatment of steel is distinct from the forging is usually used to make shapes and sizes close to the waste. The organization of the alloy cannot play a decisive role. Therefore, the final step of titanium rod process specifications has a particularly important role. It is necessary to make the overall deformation of the blank not less than 30% of the deformation temperature does not exceed the phase transition temperature, in order to make the titanium rod at the same time to obtain higher strength and plasticity and should strive to temperature and degree of deformation throughout the deformation of the rough as possible.
(4) the first rolling, at 970 ~ 980 ℃ under the conditions of a preliminary mill rolling into a cylindrical shape blank;
(5) The second rolling, under the conditions of 950, rolling into a bank in a rolling mill.
There are many rolling methods that can be ranked according to different characteristics. Extruded by metal flow and deformation characteristics of classification, a positive extrusion, reverse extrusion and special extrusion. Special extrusion includes hydrostatic extrusion, continuous extrusion, lateral extrusion, co-extrusion, coextrusion, sheath extrusion, peeling extrusion, water seal extrusion, bitter extrusion, powder extrusion, semi Melt Extrusion, liquid extrusion and the like. Extrusion by temperature classification, hot extrusion, warm extrusion and cold extrusion. Hot extrusion and cold extrusion are the two major branches of extrusion, the main application in the metallurgical industry hot extrusion, which is commonly known as the extrusion; mechanical industrial system application of cold extrusion; warm extrusion development relatively late, the scope of application is small .
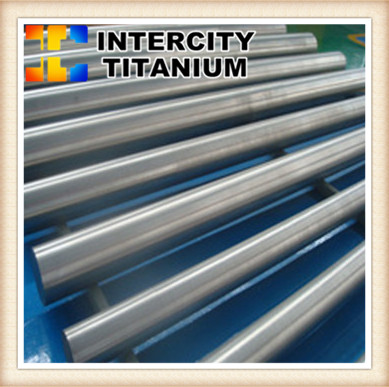